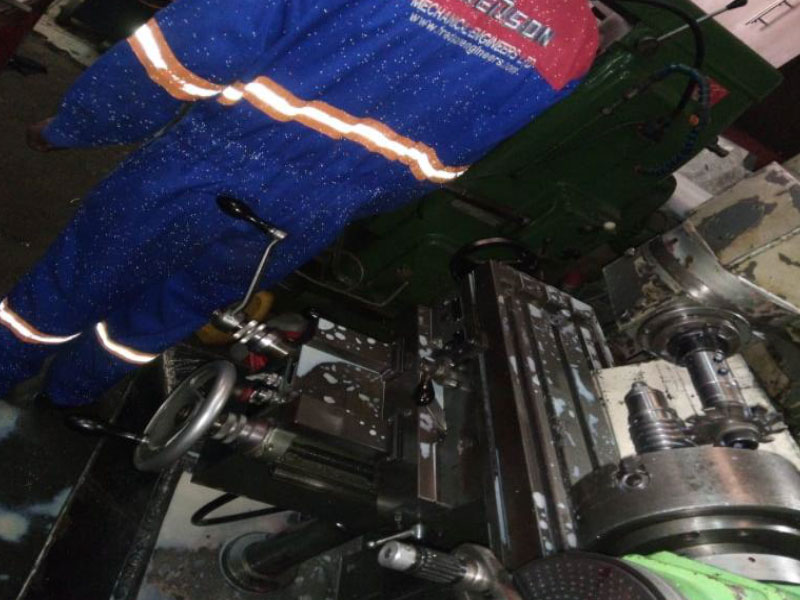
General Machining of Industrial Machinery Parts and Components.
Fredson Mechanical Engineers Ltd (FME) has invested heavily in work shop Machine Tools, and highly skilled technicians, which enables us to precisely machine new and repair various machinery parts and components. i.e Gears, Shafts etc.
We select the correct engineering material for each job and we do final treatment (Hardening and tempering) where necessary, we are able to achieve the correct degree of hardness (HRC) required for each work. We have invested in an Induction hardening facility and a state of the art Laboratory.
- Upgrade: We provide the latest Engineering Innovation and solutions helping our clients keep at par with the current technologies.
- Rebuild: Highly equipped workshop enables us to cater for our clients unique needs with attention to details as per client’s requirements.
- Repair: High quality precision machinery coupled with experienced technicians caters for all kinds mechanical and hydraulic equipment repairs.