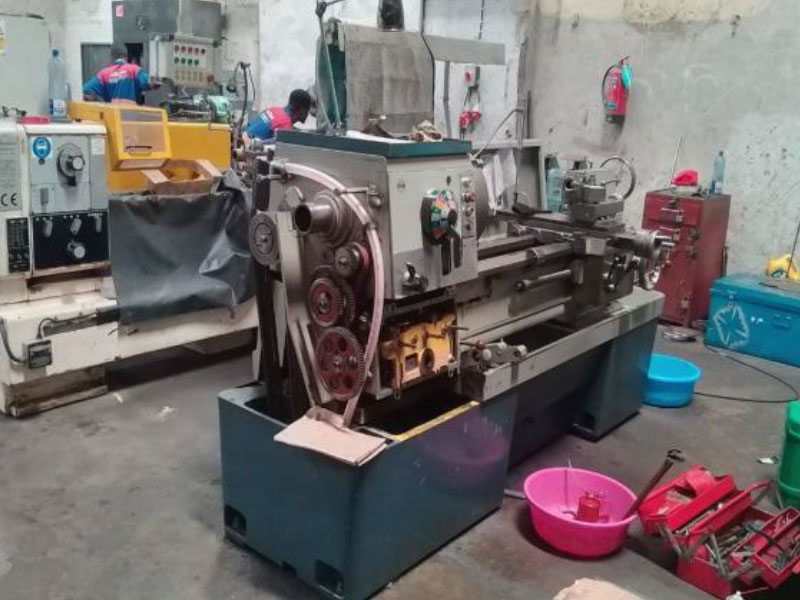
Machine Tool Repair and Maintenance
Industrial machine tool repair and maintenance is crucial for ensuring that machinery operates efficiently and has a long lifespan. Regular maintenance and timely repairs can prevent costly downtime, extend the life of the equipment, and improve productivity. Here are some key aspects of industrial machine tool repair and maintenance:
1. Preventative Maintenance:
- Routine inspections: Regular checkups can help spot early signs of wear and tear, preventing more serious damage.
- Lubrication: Ensuring that moving parts are properly lubricated to reduce friction and wear.
- Cleaning: Keeping the machinery clean to avoid buildup of dust, debris, or oil that can cause malfunctions.
- Calibration: Regularly checking and adjusting the machine for precise operation.
2. Corrective Maintenance:
- Troubleshooting: When a machine tool breaks down, identifying the cause of the problem quickly and accurately is key to reducing downtime.
- Repairs: This includes fixing or replacing worn or damaged parts such as motors, bearings, gears, or electrical components.
3. Electrical & Control Systems:
- Control panel diagnostics: Ensuring that the electrical and control systems are functioning properly is critical. Any issues with these systems can cause malfunctions or breakdowns.
- Wiring checks and upgrades: Over time, wiring may degrade, and it’s important to regularly inspect it for faults or damage.
4. Machine Component Overhaul:
- Spindle repair/replacement: Spindles can wear out over time and may need to be overhauled or replaced.
- Ball screw & linear guide repair: These are essential components that may experience wear from constant movement and load. Repairing or replacing them ensures smooth and precise operation.
5. Software & System Updates:
Many industrial machine tools are controlled by complex software. Keeping the software up to date can optimize performance and efficiency, and prevent software-related malfunctions.
6. Specialized Training:
Operators and maintenance staff need specialized training to maintain and repair the machines properly. Training ensures that they can identify issues early and perform effective repairs.
7. Spare Parts Inventory:
Keeping an inventory of critical spare parts (like bearings, belts, or seals) helps in reducing downtime as parts can be replaced quickly when needed.
8. Diagnostics Tools:
Using advanced diagnostic tools, such as vibration analyzers, thermal cameras, or laser alignment tools, can help pinpoint issues that may not be visible to the naked eye.
9. Safety Protocols:
Regular maintenance should always be conducted with proper safety measures in place, especially when dealing with high-speed or high-voltage equipment.
Is there a specific area of machine tool repair or maintenance you’re interested in? I can offer more detailed information on that if you’d like!