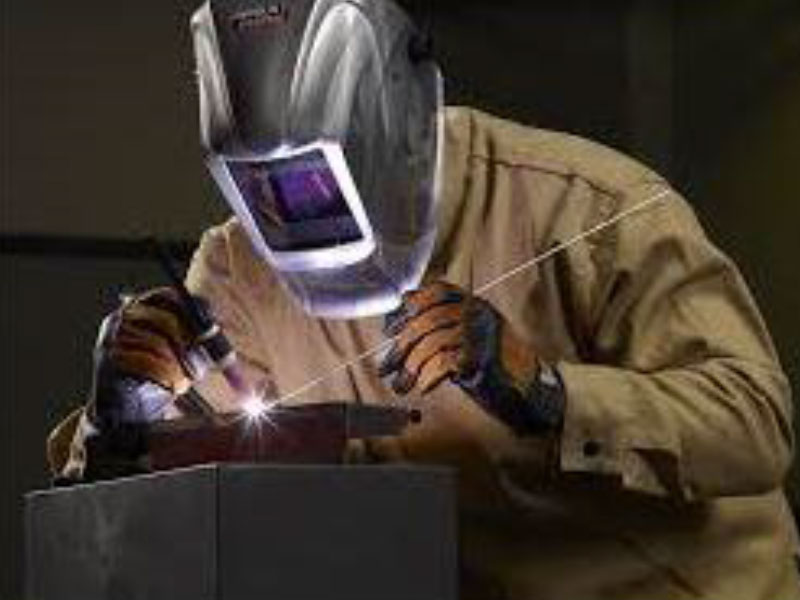
Metal Fabrication / Structures & steel erection.
Fredson Mechanical Engineers Ltd (FME) is one of the leading steel fabrication farms that specialize in the design, fabrication and erection of all structural steel works, in this region.
We are well equipped with the machinery, tools and manufacturing facility, to process and erect even much bigger steel structures i.e.
- Malty storey buildings,
- Trusses,
- Pressed panel steel water Tanks & towers,
- Steel bridges,
- Heavy industrial Plants
- Machinery installations.
- Light gauge steel frames,
- Pallet racking solutions,
- Petrol stations,
- Cow barn,
- Steel sheds,
- Poultry sheds.etc.